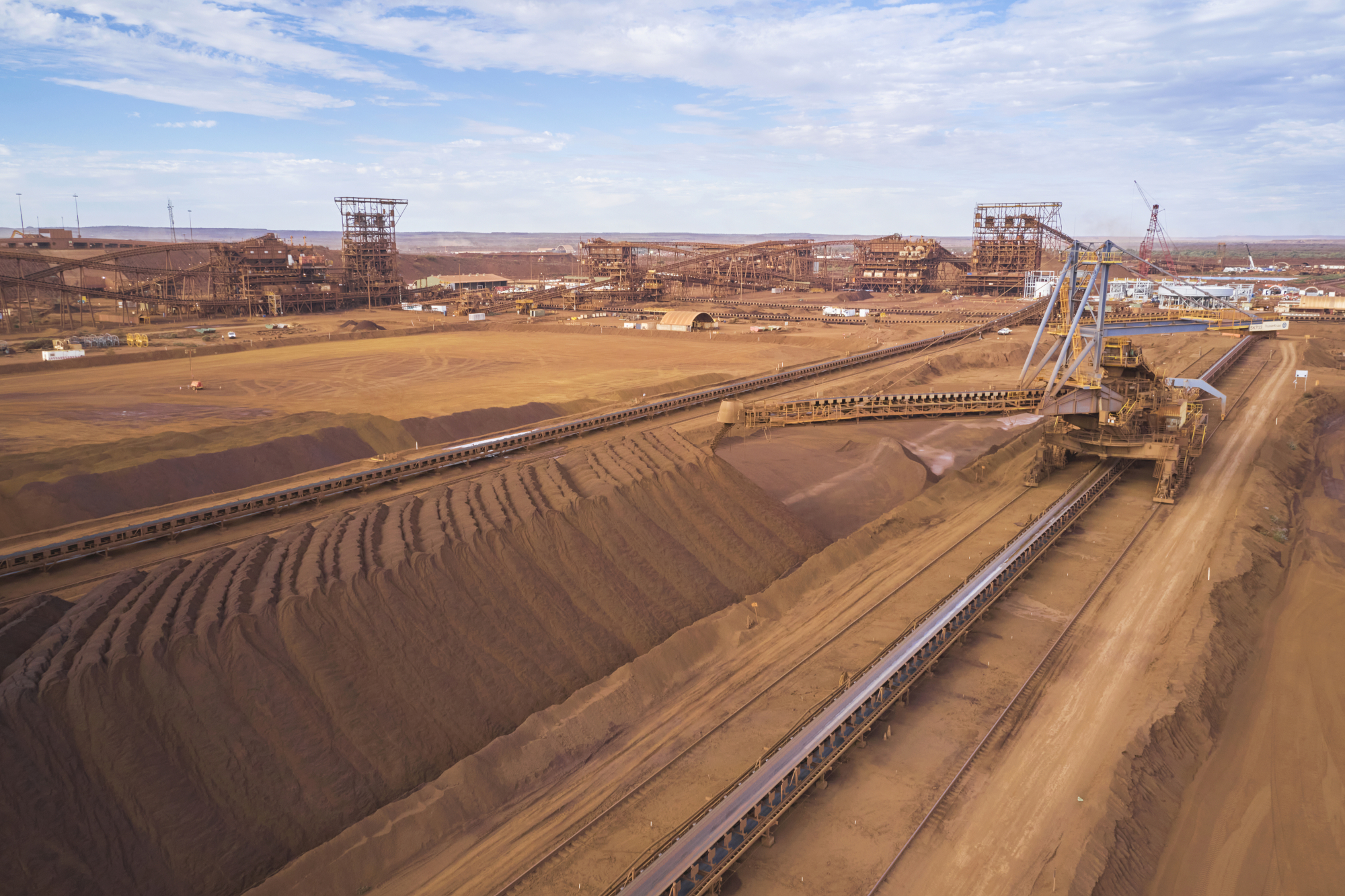
I&E Systems
We are one of Australia's leading instrument, electrical and safety system engineering companies. Located in Perth, Western Australia, we are proudly 100% Australian-owned and have been in operation since 1991.Comprehensive Project Lifecycle Support
For over 30 years, we have supported our major clients in delivering projects that span the entire engineering lifecycle. Our approach ensures that every project phase, from feasibility studies to design execution, is managed with the utmost expertise and attention to detail.
Turnkey Solutions for Every Phase
Our ‘Turnkey’ methodology encompasses implementation, construction support, commissioning, and startup, extending to ongoing operations. This holistic strategy guarantees that our clients receive consistent and comprehensive support, resulting in successful project outcomes every time.
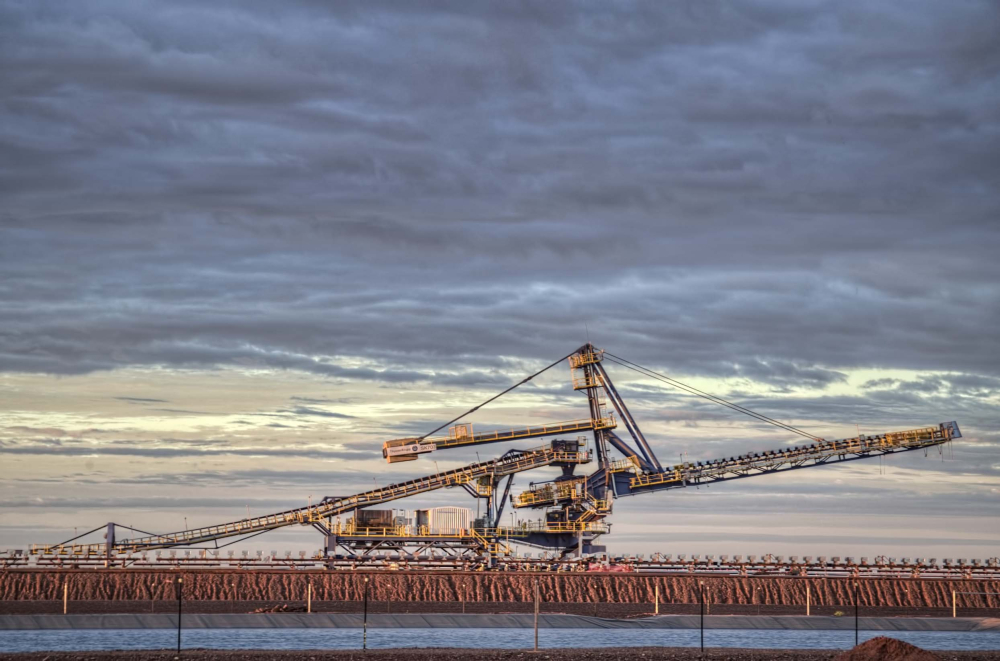
Major Clients
Woodside
- Ongoing projects since 1991, with over 500 projects from small modifications to large multiyear critical projects using a dedicated team of experts in Oil & Gas projects.
BHP
- Beginning in 1995 we have completed some projects (250+) with a strong focus in maintaining a strong team familiar with the clients needs.
Chevron
- Began in 1993 and with over 150 projects completed we maintain an excellent relationship providing ongoing support and projects.
Our other major clients
- Some major clients go back over ten years such as South 32, Inpex and Fortescue where we have delivered 100’s of projects with parts/all of the engineering lifecycle.
- Anglo Gold Ashanti Australia
- Carbon 280 Pty Ltd
- Coogee Chemicals
- DRA Pacific Pty Ltd
- Kalgoorlie Consolidated Gold Mine
- Metso Outotec Australia Limited
- NEWest Alliance
- Rail Systems Australia
- Santos Ltd
- Shell UK Ltd
Training
I&E Systems is a world leader in the field of functional safety management. I&E Systems offers Functional Safety training courses to engineers and managers.